Porosity in Welding: Identifying Common Issues and Implementing Best Practices for Prevention
Porosity in welding is a prevalent problem that typically goes undetected up until it triggers substantial issues with the integrity of welds. In this discussion, we will explore the key factors contributing to porosity development, examine its detrimental results on weld performance, and discuss the ideal methods that can be adopted to reduce porosity incident in welding processes.
Common Sources Of Porosity
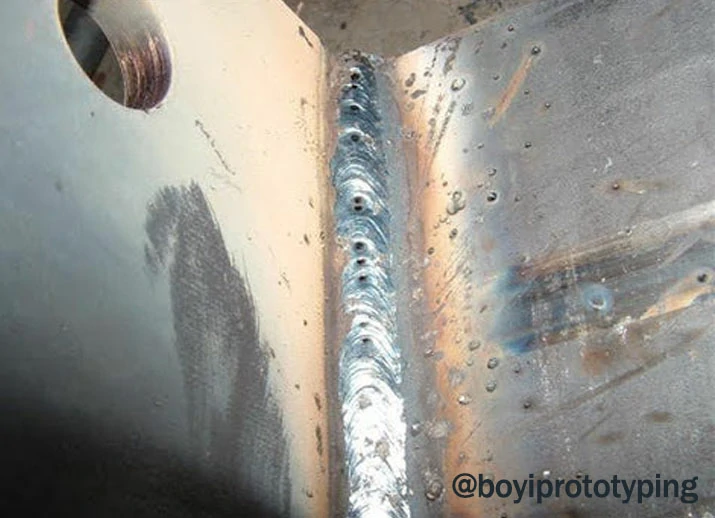
Making use of dirty or wet filler products can present contaminations into the weld, contributing to porosity problems. To reduce these usual causes of porosity, extensive cleansing of base metals, appropriate securing gas selection, and adherence to optimum welding parameters are necessary techniques in achieving premium, porosity-free welds.
Effect of Porosity on Weld High Quality

The presence of porosity in welding can significantly endanger the architectural stability and mechanical homes of bonded joints. Porosity produces voids within the weld steel, deteriorating its general strength and load-bearing capacity.
Among the main consequences of porosity is a decrease in the weld's ductility and sturdiness. Welds with high porosity degrees have a tendency to display lower impact stamina and reduced capacity to warp plastically before fracturing. This can be specifically concerning in applications where the welded parts go through vibrant or cyclic loading problems. Porosity can restrain the weld's capability to properly transfer pressures, leading to early weld failure and possible security hazards in critical frameworks. What is Porosity.
Best Practices for Porosity Avoidance
To boost the structural stability and top quality of welded joints, what particular measures can be executed to lessen the occurrence of porosity during the welding procedure? Porosity avoidance in welding is vital to make certain the integrity and strength of the last weld. One reliable practice is appropriate cleansing of the base metal, eliminating any kind read review of pollutants such as rust, oil, paint, or wetness that can lead to gas entrapment. Making sure that the welding tools remains in good condition, with tidy consumables and appropriate gas flow prices, can additionally dramatically reduce porosity. Furthermore, keeping a secure arc and controlling the welding parameters, such as voltage, current, and travel speed, assists produce a regular weld swimming pool that decreases the threat of gas entrapment. Making use of the correct welding technique for the certain product being bonded, such as adjusting the welding angle and gun position, can even more stop porosity. Regular evaluation of welds and instant removal of any type of concerns determined throughout the welding process are vital methods to stop porosity and generate top quality welds.
Value of Appropriate Welding Techniques
Carrying out proper welding techniques is paramount in ensuring the structural integrity and quality of welded joints, developing upon the structure of effective porosity prevention procedures. Too much heat can lead to boosted porosity due to browse around here the entrapment of gases in the weld swimming pool. Additionally, making use of the appropriate welding specifications, such as voltage, existing, and travel speed, is vital for attaining sound welds with minimal porosity.
Moreover, the selection of welding procedure, whether it be MIG, TIG, or stick welding, should align with the particular requirements of the project to make sure ideal results. Correct cleaning and prep work of the base metal, as well as selecting the best filler material, are likewise necessary parts of proficient welding techniques. By adhering to these best practices, welders can reduce Extra resources the danger of porosity formation and create top notch, structurally sound welds.

Testing and High Quality Control Procedures
Quality assurance measures play a vital duty in validating the integrity and reliability of welded joints. Checking treatments are vital to discover and stop porosity in welding, making certain the toughness and resilience of the end product. Non-destructive testing methods such as ultrasonic testing, radiographic testing, and visual inspection are commonly employed to identify potential problems like porosity. These techniques permit the assessment of weld quality without endangering the integrity of the joint. What is Porosity.
Performing pre-weld and post-weld evaluations is additionally important in maintaining top quality control requirements. Pre-weld evaluations involve validating the materials, tools setups, and cleanliness of the workspace to avoid contamination. Post-weld assessments, on the other hand, analyze the final weld for any kind of flaws, including porosity, and verify that it meets specified criteria. Implementing a thorough high quality control strategy that includes detailed testing treatments and evaluations is extremely important to decreasing porosity concerns and guaranteeing the total quality of bonded joints.
Final Thought
To conclude, porosity in welding can be an usual issue that impacts the high quality of welds. By recognizing the common reasons for porosity and carrying out ideal techniques for avoidance, such as proper welding methods and testing procedures, welders can make sure top quality and reliable welds. It is necessary to prioritize prevention techniques to reduce the incident of porosity and keep the honesty of bonded frameworks.
Comments on “What is Porosity in Welding: Finest Practices for Staying Clear Of Porous Welds”